AI/HPC時代封裝革命:解析TC-NCF、MR-MUF與Hybrid Bonding三大關鍵技術
- Kimi
- 6天前
- 讀畢需時 9 分鐘
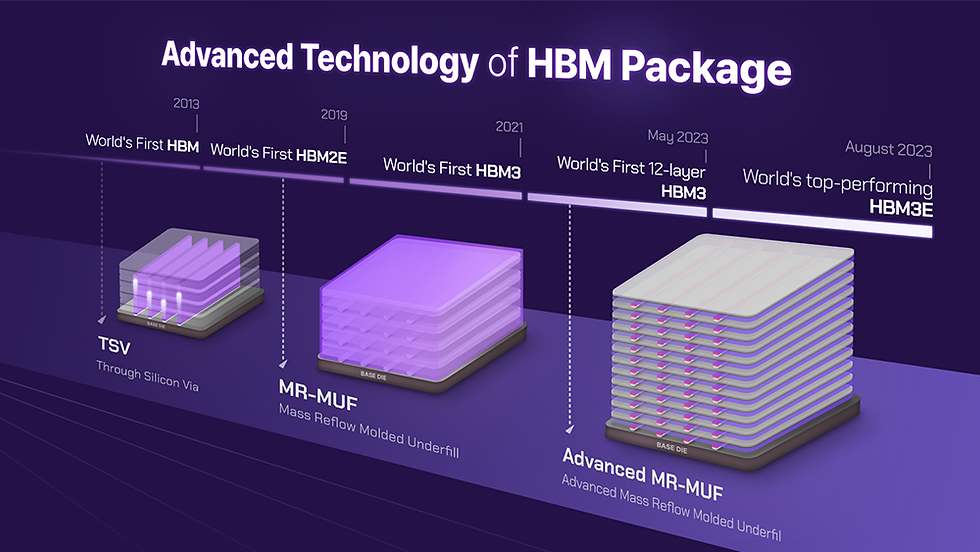
隨著人工智慧(AI)與高效能運算(HPC)時代來臨,封裝技術已經不再只是簡單地「把晶片裝到基板上」而已,而是講求高度整合、高頻寬、高散熱與更高的可靠度。近年來圍繞著高頻寬記憶體(HBM)的話題越來越夯,三大DRAM原廠(Samsung、SK hynix、Micron)為了讓晶片堆疊層數更多、速度更快,同時兼顧良率與散熱,便各自發展出三種最受矚目的先進製程技術:TC-NCF、Hybrid Bonding、以及MR-MUF。
一、封裝從「微凸塊」到「混合鍵合」的演進脈絡
在既有的2D封裝或是傳統的線架構封裝中,因為對I/O密度與堆疊層數的需求有限,多半使用一般的銲線(Wire Bonding)或倒裝晶片(Flip Chip Bonding)就能達到目標。然而,面對AI、大數據與雲端運算的暴增需求後,越來越多的先進產品(特別是HBM)必須在有限的封裝高度下,堆疊更多層DRAM,並提供更高頻寬與更好的散熱。
這時候,**微凸塊(Micro Bump)**技術便扮演了重要角色:在每顆DRAM晶粒間或晶粒與基板間,透過細小的凸塊來連接。但當凸塊間距越縮越小、層數越堆越高,原本的TC-Bonder、倒裝晶片等方式也出現了極限,尤其在散熱、良率和可靠度上。
因此,業界陸續提出了TC-NCF(Thermal Compression with Non-Conductive Film)、**MR-MUF(Mass Reflow - Molded Underfill)以及Hybrid Bonding(混合鍵合)**這三大關鍵方案,試圖突破傳統封裝的瓶頸。
二、TC-NCF:利用「非導電膜」熱壓接合,工法成熟度高
1. 什麼是 TC-NCF?
TC-NCF(Thermal Compression with Non-Conductive Film)是一種熱壓接合技術,透過在晶圓或晶粒表面預先塗佈非導電膜(NCF),再以高溫高壓方式將晶片的微凸塊(或銅柱加錫帽)與基板/下層晶片可靠接合。這時,NCF在加熱過程中融化,填補空隙並固化,形成電氣連接與機械支撐的一次性製程。
2. 優勢與應用
適合細間距、高密度
TC-NCF可應用於小於 20μm 的間距,能對應極高I/O密度,特別適用於HPC、AI晶片或3D封裝等先進應用。
減少製程步驟
NC*F 在熱壓時同時完成電氣接合和底部填充功能,可免去後續額外的底部填充流程,縮短生產時間。
降低熱應力
NCF在晶粒與基板間扮演「緩衝」角色,有助於抑制熱膨脹係數(CTE)差異,提升整體封裝可靠度。
高階應用廣泛採用
Samsung、Micron等廠商在HBM (High Bandwidth Memory)的量產導入TC-NCF工藝,成為高密度先進封裝的重要利器。
3. 微凸塊(Micro Bump)與TC-NCF的差別
連接方式
微凸塊(Micro Bump):可視為倒裝晶片技術的進階版,使用極小的凸塊(10~50μm)支援高密度互連,常用於2.5D/3D封裝與HBM中。
TC-NCF:是一種「熱壓 + 非導電膜」的高精度工藝,需搭配微凸塊或銅柱才能在極細間距下達到精準且可靠的鍵合。
填充方式
微凸塊:一般先回流焊形成電性接合,再額外加入底部填充(Underfill)強化封裝強度。
TC-NCF:則在壓合前就塗佈非導電膜(NCF),並於熱壓同時完成電氣連接與空隙填充,簡化流程。
間距與精度
微凸塊:可做到10~50μm,若須更精細則需更嚴格的工藝控制。
TC-NCF:透過熱壓與NCF的結合,能有效降低橋接風險並支援 <20μm 的超細間距。
應用
微凸塊:廣泛應用於3D/2.5D封裝,以及各種需要高頻寬、高密度互連的先進晶片。
TC-NCF:常用於HBM、GPU、AI/HPC加速器等精細封裝中,能同時滿足高密度、散熱與量產需求。
4. 回流焊(Mass Reflow) vs. 熱壓技術(TC-NCF)
回流焊(Mass Reflow)與TC-NCF皆為常見的先進封裝接合技術,但兩者適用範圍、工藝模式和成本結構差異明顯:
特性 | 回流焊 (Mass Reflow) | 熱壓技術 (TC-NCF) |
接合原理 | 焊料熔化→自然固化 | 高溫高壓 + 預先塗佈NCF |
溫度範圍 | 約220~260°C (依焊料種類) | 約200~300°C (視材料、壓力而定) |
壓力 | 不需外加壓力 | 需穩定且精確的加壓 |
填充材料 | 回流後再做底部填充(Underfill) | NCF一次到位,熱壓同時完成機械支撐與電氣連接 |
間距適用性 | 中等間距(>50μm) | 超細間距(<20μm) |
產量 / 效率 | 一次能處理多顆,量產效率高 | 一次處理單顆或少量,產能較低 |
對位要求 | 中等(透過焊料熔化可自對準) | 極高(需高精度熱壓對位設備) |
設備 & 成本 | 傳統設備較成熟,整體成本較低 | 設備昂貴,工藝複雜,對高性能與高附加價值封裝更划算 |
典型應用 | 一般Flip Chip封裝、SMT大批量 | 3D/2.5D先進封裝(HBM、AI/HPC、高速I/O) |
回流焊(Mass Reflow)
優點:成熟度高、可大規模生產、製程與設備成本相對較低。
缺點:無法支援超細間距,且後續必須增設底部填充工序。
TC-NCF(Thermal Compression + Non-Conductive Film)
優點:支援<20μm間距、高I/O密度、無需後段底部填充;NCF能在熱壓時一併填充縫隙,提升散熱與可靠度。
缺點:對位精度和設備要求高,單次處理量少,整體成本較高。
三、MR-MUF:一次解決「連線 + 填充 + 散熱」
MR-MUF(Mass Reflow Molded Underfill)是近期備受注目的先進封裝技術,結合「回流焊」與「環氧模塑化合物(EMC)」,能同時完成晶片連線與封裝填充,特別適用在高層數、高頻寬且散熱需求極高的應用,如 HBM(High Bandwidth Memory)。
1. 回流焊(Mass Reflow)與 MR-MUF 的差異
回流焊(Mass Reflow)
定義:先將焊膏塗布於基板,再透過回流爐加熱,使焊料(錫鉛或無鉛)達到熔點,讓晶片凸點與基板焊墊形成連接。
特點:
接合後通常還需另行「底部填充(Underfill)」;
適合大批量生產,但在散熱與結構強度上較無法一次兼顧。
MR-MUF 與回流焊之間的不同
填充方式:回流焊後必須再做底部填充;MR-MUF則在回流過程中同時以環氧模塑化合物(EMC)填充縫隙並包覆外部,一次完成接合與填充。
製程整合:回流焊僅執行銲接,MR-MUF 直接把「回流 + 模塑填充」整合成一個流程,省時高效。
散熱表現:MR-MUF 使用高導熱 EMC,相較於傳統回流焊可大幅提升散熱,如 HBM2E 相較 HBM2 約提升 36% 散熱效能。
應用範疇:回流焊常用於一般倒裝晶片;MR-MUF 更適合高整合度、多層堆疊的先進應用(如 HBM)。
2. 熱壓技術(TC-NCF)與 MR-MUF 的差異
熱壓技術(TC-NCF)
定義:在晶圓或基板預先放置非導電膜(NCF),再以高溫高壓將晶片凸點與基板接合。
特點:
能對超細間距(<20μm)進行高精度封裝;
產量、速度較受限,成本偏高。
MR-MUF 與 TC-NCF 的差別
接合方式:
TC-NCF 靠熱壓機機械壓合;
MR-MUF 則使用回流爐熔化凸點並注入 EMC。
填充材料:
TC-NCF 採用非導電膜,導熱度較低;
MR-MUF 透過 EMC,擁有更高散熱與整體保護。
產量與成本:
TC-NCF 適合小批量、精密應用;
MR-MUF 在大規模量產與散熱表現上更具優勢。
應用場景:
TC-NCF 多見於超微間距封裝;
MR-MUF 更適用像 HBM 這類高層堆疊、高散熱需求領域。
3. MR-MUF(Mass Reflow Molded Underfill)的核心特性
MR-MUF 將傳統的「回流焊」升級為「一次性電氣連接 + 同步模塑填充」,在一個回流製程中完成高密度接合與 EMI(電磁干擾)/熱管理等要求。
製程步驟:
晶片預先對位於基板;
回流爐升溫,使凸點熔化並形成電氣連結;
同步注入 EMC 填充間隙並外部包覆固化。
三大優勢:
高散熱:EMC 常含高熱傳填料,更適合高功耗應用;
省工序:無需再做後加底部填充,一氣呵成;
支撐度佳:適合多層堆疊(如 12 層、16 層 HBM),控制晶片翹曲問題。
潛在挑戰:
高溫回流恐導致晶片翹曲,需搭配先進補償設計;
EMC 材質必須保證空隙率極低並具有足夠流動性。
【補充】EMC模塑 vs. 底部填充(後加)
EMC 模塑:
範圍:可同時填充晶片縫隙並包覆外部;
材料:環氧樹脂(Epoxy)+ 填料,導熱度高(1~3W/m·K);
製程:一次模塑固化,保護性高且散熱佳;
應用:如 MR-MUF,適用於高功耗、高密度堆疊(如 HBM)。
底部填充(Underfill,後加):
範圍:僅針對晶片與基板間隙;
材料:以毛細作用填充的環氧膠,導熱度較低;
製程:多一步驟,接合後再進行點膠、固化;
應用:一般 Flip Chip,常用於間距中等或較細的環境,但整體散熱不如 EMC。
4. Hybrid Bonding:移除凸塊,真正邁入銅對銅「混合鍵合」
Hybrid Bonding(混合鍵合)是一種無焊料的先進封裝技術,透過在晶圓或晶粒表面進行**銅對銅(Cu-to-Cu)**直接鍵合,同時結合介電層(如SiO₂)等分子鍵合,能達成超細間距、高I/O密度的3D整合。
1. EMC模塑(Epoxy Molded Compound)與 Hybrid Bonding 的差別
EMC模塑(Epoxy Molded Compound)
定義:利用環氧模塑化合物(EMC)經高溫高壓注入並固化,在晶粒與基板或堆疊模組之間,形成整體包覆與支撐。
製程:先完成晶粒或凸塊接合,再藉由模塑(Molding)設備將EMC灌入並固化。
互連方式:透過焊料凸塊(如倒裝晶片凸塊)或微凸塊實現電氣連接,EMC僅作為填充與防護材料。
EMC模塑 vs. Hybrid Bonding
互連方式:EMC模塑需要焊料或凸塊;Hybrid Bonding為銅對銅直接鍵合,無須凸塊。
間距:EMC模塑一般在 >20μm;Hybrid Bonding可小於10μm,甚至1μm以下。
填充材料:EMC模塑需環氧樹脂填充;Hybrid Bonding不須額外填充,靠晶片表面直接貼合。
性能:EMC雖有不錯的散熱與保護,但寄生電感和電阻較高;Hybrid Bonding電氣與散熱效能更佳。
應用:EMC模塑常見於HBM或多晶片SiP;Hybrid Bonding用於最尖端的3D IC或高效能運算晶片。
2. 底部填充(Underfill,後加)與 Hybrid Bonding 的差別
底部填充(Underfill,後加)
定義:在倒裝晶片或微凸塊電氣連接後,透過液態環氧樹脂的毛細作用填充晶片與基板空隙,最終固化成型。
製程:「先接合,後填充」,利用點膠或噴塗,灌進間隙中增強機械穩定度。
互連方式:依舊靠焊料或微凸塊來做電性連接,Underfill只作支撐。
底部填充 vs. Hybrid Bonding
互連方式:底部填充需要焊料凸塊;Hybrid Bonding是Cu-to-Cu直接接觸。
間距:底部填充能應付 <20μm;Hybrid Bonding可進一步達到 <1μm超細間距。
填充需求:底部填充要額外灌膠;Hybrid Bonding則不需要,晶圓表面直接鍵合。
製程複雜度:底部填充只多加一道後填步驟,較為簡單;Hybrid Bonding需高度CMP平坦、精密對位,整體難度和成本都更高。
應用:底部填充多見於倒裝晶片、微凸塊封裝;Hybrid Bonding則鎖定先進3D整合與HPC/AI領域。
3. Hybrid Bonding(混合鍵合)的特點
定義:透過銅墊(Cu Pad)對銅墊,以及介電材料的直接鍵合,同步實現電性和機械連接。
製程步驟:
晶圓表面CMP(化學機械拋光)以獲得極高平坦度。
在高度潔淨、精密對位的環境下使銅墊與介電層對齊。
在相對低溫(<400°C)與適度壓力下實施鍵合,銅墊形成金屬鍵,介電層產生共價鍵。
優點:
可達超細間距(<1μm),I/O密度高。
無需凸塊或焊料,寄生電感/電阻極低,訊號與功耗表現出色。
無填充材料,散熱更有效。
缺點:
工藝複雜,對表面平坦度、潔淨度和對位精度要求極高。
設備與材料成本高、初期良率不易提升。
目前主要用於高階AI/HPC與先進3D封裝市場。
4. 三者簡易比較表
特性 | EMC模塑(Epoxy Molded Compound) | 底部填充(Underfill, 後加) | Hybrid Bonding(混合鍵合) |
互連方式 | 焊料凸塊 + EMC全包覆 | 焊料凸塊 + Underfill填充 | 銅對銅(Cu-to-Cu)直接鍵合 |
填充材料 | EMC(整體包覆) | Underfill(局部底部填充) | 無需(晶片表面直接接合) |
間距適用性 | 中高(>20μm) | 細(<20μm) | 超細(<1μm) |
散熱性能 | 較優(1~3 W/m·K) | 一般(0.2~0.8 W/m·K) | 良好(銅互連,低熱阻) |
電氣性能 | 普通(有寄生效應) | 依凸塊規格而異 | 極佳(超低損耗/電感) |
製程複雜度 | 中等(模塑設備) | 低(僅多一步點膠固化) | 高(CMP、對位精度、潔淨度要求) |
保護能力 | 整體保護 | 局部底部支撐 | 無外部保護,需搭配其他包覆 |
成本 | 中高 | 低 | 高 |
主要應用 | HBM、多晶片SiP封裝 | 倒裝晶片、微凸塊封裝 | 高階3D整合、高效能運算及AI晶片 |
五、展望:AI 帶動先進封裝再進化
AI、大數據、雲端運算持續成長由於各家對巨量資料的演算需求急遽攀升,HBM這類高頻寬記憶體對整個算力的提升至關重要。未來對封裝高度、熱管理的要求越來越嚴苛,也逼著各大封裝廠、IDM廠加快腳步在TC-NCF、MR-MUF及混合鍵合中做出最適合的選擇。
台積電、三星、Intel分進合擊在異質整合(Heterogeneous Integration)與先進封裝領域,台廠(例如台積電以CoWoS、SoIC、InFO等技術)具備強大影響力。三星也同樣積極推進自家I-Cube與X-Cube,Intel則以EMIB與Foveros為武器。未來,隨著混合鍵合技術愈趨成熟,整合「基底裸晶+HBM」的方式,可能會成為新的商業模式。
供應鏈策略重整封裝製程從微凸塊(Bump)走向無凸塊銅互連,整個後段生態供應鏈也會洗牌:設備廠商、化學材料、封裝測試服務,都會面臨新的機會與挑戰。尤其當良率與成本壓力浮現,誰能及早在「新世代封裝」站穩腳跟,誰就能在AI浪潮中脫穎而出。
六、結語
TC-NCF、MR-MUF與Hybrid Bonding,分別代表了三種不同程度的先進封裝思維與路線:
TC-NCF:成熟度高,但在散熱與堆疊層數上有所限制;
MR-MUF:改善散熱、一次回流,工序效率高,SK hynix憑此在HBM市場市佔領先;
Hybrid Bonding:移除凸塊、提升I/O密度與堆疊層數,被視為未來HBM4 16hi、HBM5 20hi的主流方案,但仍有高成本與良率關卡待克服。
對台灣來說,從IC設計、晶圓代工到後段封測的完整供應鏈,在這波封裝技術升級中具有關鍵地位。無論是採用TC-NCF、MR-MUF還是Hybrid Bonding,各家業者都在尋求「更快、更薄、更省電」的最佳解方,這也就是新世代封裝的核心意義。面對AI與高效能計算的爆炸性需求,新一輪的「封裝革命」才正要開始。
Comments